Is On-Site Nitrogen & Oxygen Generation the Key to Cutting Costs and Improving Quality for Businesses?
Laser cutting, a technology that emerged in the 1960s, has transformed the sheet metal industry. Its roots can be traced back to the aircraft manufacturing industry, but today, it spans the gamut from giant automobile plants to niche nameplate engraving businesses. The evolution of laser-cutting technology has been relentless, ascending to unprecedented levels of precision, operational ease, speed, and integration with Industry 4.0 technologies. One incontrovertible fact remains: laser cutting presents both direct and indirect monetary benefits, relegating traditional cutting methods to the past. Reduced labour costs and minimal material wastage are compelling reasons for the industry's widespread adoption of this transformative technology. Yet, as we venture into the field of higher kilowatt (KW) Fiber laser cutting machines, capable of slicing through tough, thick metals like stainless steel and aluminium sheets nearing 1.5 inches at astonishing speeds, a new challenge emerges. The voracious appetite for cutting gases such as Nitrogen and Oxygen, integral to the laser cutting process, is undeniable. Adding complexity to the equation, the continuous ascent of Nitrogen and Oxygen prices by external gas companies and lingering supply chain challenges have left the laser-cutting industry at a crossroads. The need for a more reliable and cost-effective solution is paramount. This blog explores how on-site Nitrogen and Oxygen generation holds the key to not only managing costs but also elevating the quality of laser cutting in the modern business landscape.
In the world of laser cutting, challenges related to cutting gases like Nitrogen (N2) and Oxygen (O2) have a habit of piling up—challenges that demand an innovative response. The solution? It's time for the laser cutting industry to seize its own destiny, becoming self-sufficient by embracing on-site Nitrogen and Oxygen Generators. As the saying goes, "One Size Does Not Fit All," and this holds true for on-site gas generation as well. A comprehensive understanding of gas demands, the nature of cutting materials, required cutting pressures, and gas purity levels is essential. When it comes to designing a system for Nitrogen and Oxygen Generation, businesses should look beyond generic operational manual references. Why? Because in many cases, the cutting gas requirements stated in manuals are far from accurate, often overestimating needs. We're talking figures as high as 80 plus cubic feet per minute (CFM) at 99.999% purity. What's the key to a solution that fits like a glove? A detailed Demand Analysis, tailored to your specific requirements. It's a strategy that allows you to design a Nitrogen and Oxygen Generation system that aligns perfectly with your needs, steering you clear of unnecessary costs and inefficiencies.
Let's embark on a journey to understand the intriguing world of gas purity and how it dynamically adapts to the unique demands of end users. Gas purity isn't just a technicality; it's a cornerstone of the precise artistry performed by a laser-cutting machine. And this artistry differs dramatically from the meticulous crafting of high-end stainless-steel appliances to the rugged functionality of auto parts that will ultimately be welded into larger assemblies. Imagine this: you're utilizing gas delivered by an external company, arriving in the customary forms of cylinders, Dewars, or liquid nitrogen tanks. Typically, these deliveries adhere to predefined purity standards mandated by the gas companies. As a user, you're handed a predetermined purity level with no control over the matter. It's like paying a premium for Nitrogen with a dazzling 99.999% purity when your specific application might only require a modest 99%. Or, it could be the reverse, where you're left with less pure gas than needed, jeopardizing the quality of your cuts. Here is an example of how Nitrogen purity can influence the quality of cut by a laser cutting machine:
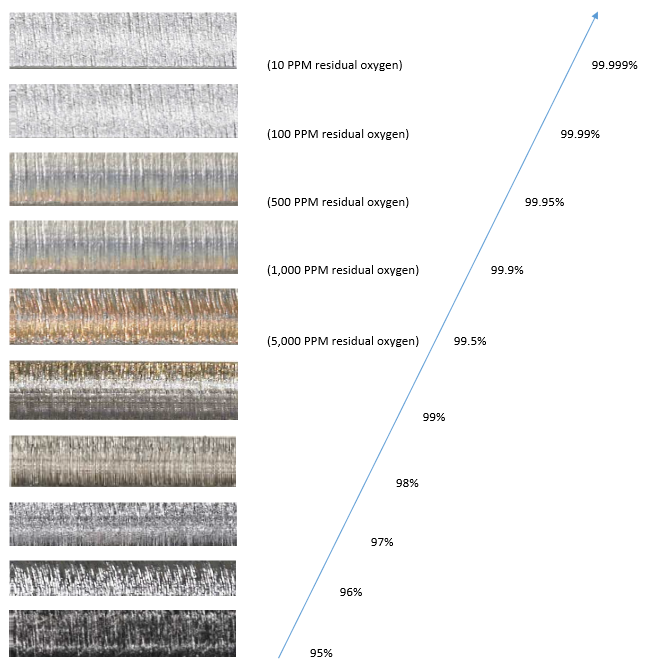
Now, envision the alternative approach: embarking on on-site nitrogen generation, giving you complete control of the helm. Let's delve into the Peak Nitrogen Generator as an illustration, providing a spectrum of purity options ranging from 95% to an astounding 99.9995%. This transformative technology puts you firmly in the driver's seat, allowing you to fine-tune the nitrogen gas purity to your exact specifications. What's even more remarkable is the system's ability to adapt purity levels on-site, eliminating any worries about modifying the generator itself, all while curbing oxidation concerns.
In the intricate dance of designing a nitrogen/oxygen generation system for laser cutting, understanding the flow required to fuel these precision machines takes centre stage. Strikingly, not all lasers are created equal, despite sharing the same kilowatt (KW) rating. Why? Because laser cutting's versatility spans a spectrum of materials and varying thicknesses. Laser operators skillfully choose nozzle sizes based on software requisites, resulting in flow requirements that can fluctuate from as low as 10 cubic feet per minute (CFM) to a robust 60 plus CFM. Our image below vividly illustrates the theoretical nitrogen consumption of a laser-cutting machine across different pressures and with diverse nozzle sizes.
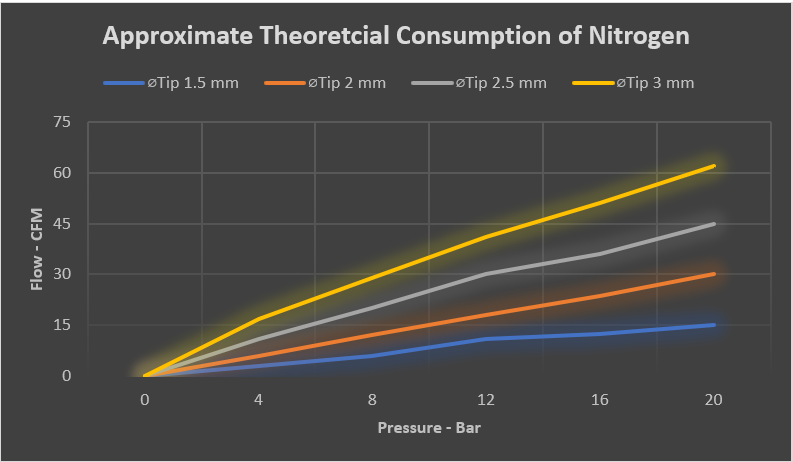
It's a visual reminder that the flow variable is indeed fluid, adapting to each unique cutting task. Many sheet metal facilities gravitate toward a consistent menu of product demands, cutting similar materials day in and day out, with infrequent nozzle changes. For these scenarios, a meticulous Demand Analysis is highly recommended to pinpoint precise flow requirements, aligning the system design accordingly. The right design for an on-site generation system is the linchpin for operational success, and it's a task best entrusted to the professionals. A comprehensive study carried out by experts ensures that your system is flawlessly tuned to your business's needs. Below, you'll find a glimpse of the results from a Nitrogen Demand Analysis conducted at a laser cutting facility in Ontario, Canada, underscoring the practical significance of this approach.
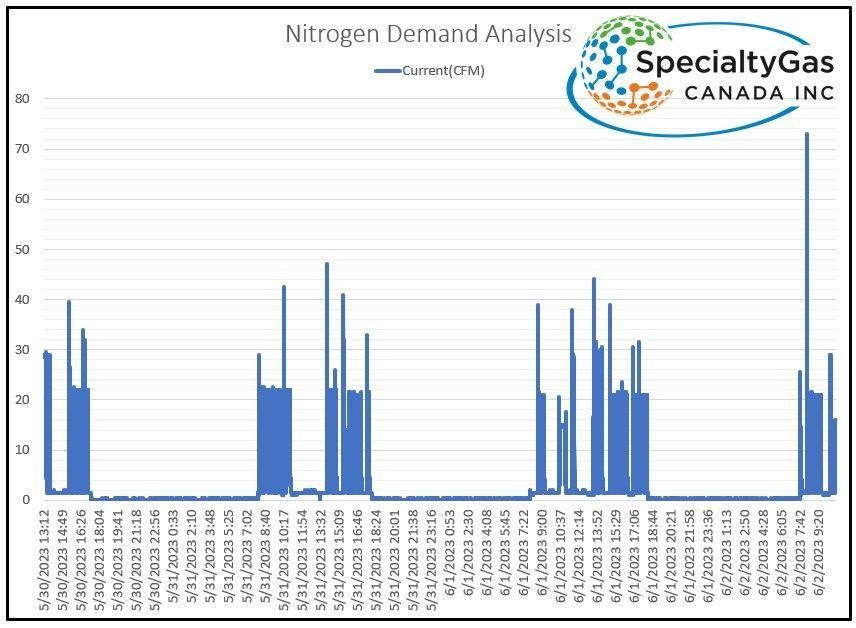
In the world of laser cutting, achieving self-sufficiency in gas generation isn't a one-note melody; it's a symphony of elements harmonizing perfectly to create the desired result. While the generators themselves (be it for Nitrogen or Oxygen) are a crucial part of this orchestration, they are not the sole stars. To bring this composition to life, a precisely sized compressed air system must take centre stage. This ensemble comprises an air compressor, air dryer, filtration system, Nitrogen Booster or Oxygen Booster, storage tanks, and meticulously calibrated piping. Each component plays a pivotal role in the success of the complete solution. Laser cutting necessitates high-pressure gas in the range of 200 to 500 psi. The importance of selecting each equipment piece with precision cannot be overstated. For instance, when achieving a final gas pressure exceeding 400 PSI, it's prudent to pair this with an air compressor rated at 150 psi or above. Why? This optimized combination ensures an ideal compression ratio, allowing the booster to seamlessly elevate gas pressure from low to high. Consider, for example, laser applications that require only 175 to 190 PSI Nitrogen pressure for sheet metal cutting. Kaeser’s 217 PSI screw air compressors prove to be the ideal matchmakers, guaranteeing a consistent supply of high-quality nitrogen gas to fuel your laser cutting ambitions.
A thoughtfully designed On-Site Nitrogen or Oxygen Generation system for laser cutting doesn't just offer a single benefit; it opens the door to a treasury of advantages for the sheet metal industry.
- Cost Benefits: The foremost benefit revolves around cost savings. Consider this: gas companies typically charge a hefty 50 cents per cubic meter (m3) for Nitrogen. In stark contrast, high-pressure Nitrogen can be produced on-site for as low as 6 cents per m3. It's a substantial reduction that directly bolsters your bottom line.
- Inflation Resilience: The second benefit offers a welcomed peace of mind. Inflation can be a formidable adversary, especially in the realm of delivered Nitrogen and Oxygen gases. On-site generation acts as a safeguard, shielding your operation from the unpredictable price surges that external suppliers can impose.
- No Contracts: For small to medium-scale sheet metal industries, navigating complex legal contracts with multinational gas giants can be a formidable task. On-site generation, however, aligns perfectly with the entrepreneurial spirit that drives many of these businesses. It eliminates the need for complex contracts and puts you in complete control. You produce the gases precisely when you need them, without fear of the dreaded "Force Majeure" clause that gas companies invoke when gas requirements fall below agreed minimums. With on-site generation, you pay only for what you need.
- Environmental Impact: By producing your own gases on-site, you join the league of environmentally conscious businesses. No more reliance on gas deliveries means a significant reduction in carbon emissions. In an era where environmental responsibility is paramount, this move is not just a cost-saving strategy but also a significant step toward reducing your carbon footprint.
- Quality Control: When you generate gases in-house, you wield precise control over their purity and consistency. This control translates to higher quality cuts, vital for industries such as aerospace, automotive, and electronics, where precision is non-negotiable.
- Dependable Supply: The COVID-19 pandemic revealed the vulnerability of supply chains. On-site generation ensures a dependable supply of essential gases, mitigating the risks associated with external disruptions. Whether your gas needs are continuous or intermittent, on-site generation adapts to your requirements with unwavering reliability.
- Customization: Your gas needs are unique, and one-size-fits-all solutions often fall short. On-site generation allows for a tailored approach, from adjusting gas purity to accommodating fluctuations in flow requirements. Your gas generation system adapts to your specific demands, ensuring that you receive precisely what you need, no more and no less.
In the realm of sheet metal fabrication, where precision and efficiency stand as paramount objectives, the adoption of On-Site Nitrogen and Oxygen Generation signifies more than a mere modernization; it represents a revolutionary leap into the future. The benefits it offers span financial savings, environmental stewardship, operational excellence, and unprecedented control. Through the utilization of a nitrogen generator, the production of nitrogen gas becomes an integral part of your operations, eliminating the need for reliance on external sources and the associated costs. This shift not only results in cost reduction but also aligns your business with the imperative of environmental responsibility, as it curtails the carbon footprint traditionally associated with compressed air and external gas sources. The quality of metal cuts attains an unparalleled level, meeting the rigorous demands of precision-centric industries.
In the face of global supply chain uncertainties, nitrogen (N2) and oxygen (O2) generation on-site provides a dependable supply of essential gases, establishing a safety net during times of disruption. Liberated from the constraints of intricate contracts, this approach affords operational flexibility. Your nitrogen and oxygen generation system evolves beyond a mere component; it transforms into a bespoke tool crafted to meet your unique requirements. In the pursuit of elevated quality, efficiency, and profitability, On-Site Nitrogen and Oxygen Generation serves as the guiding compass. It symbolizes a commitment to a greener, more precise, and self-reliant future, addressing the growing imperative of environmental responsibility. As we navigate the myriad benefits on this journey, it becomes evident that the pathway to a more sustainable, efficient, and profitable sheet metal business commences right here.
Share This Article With Your Network
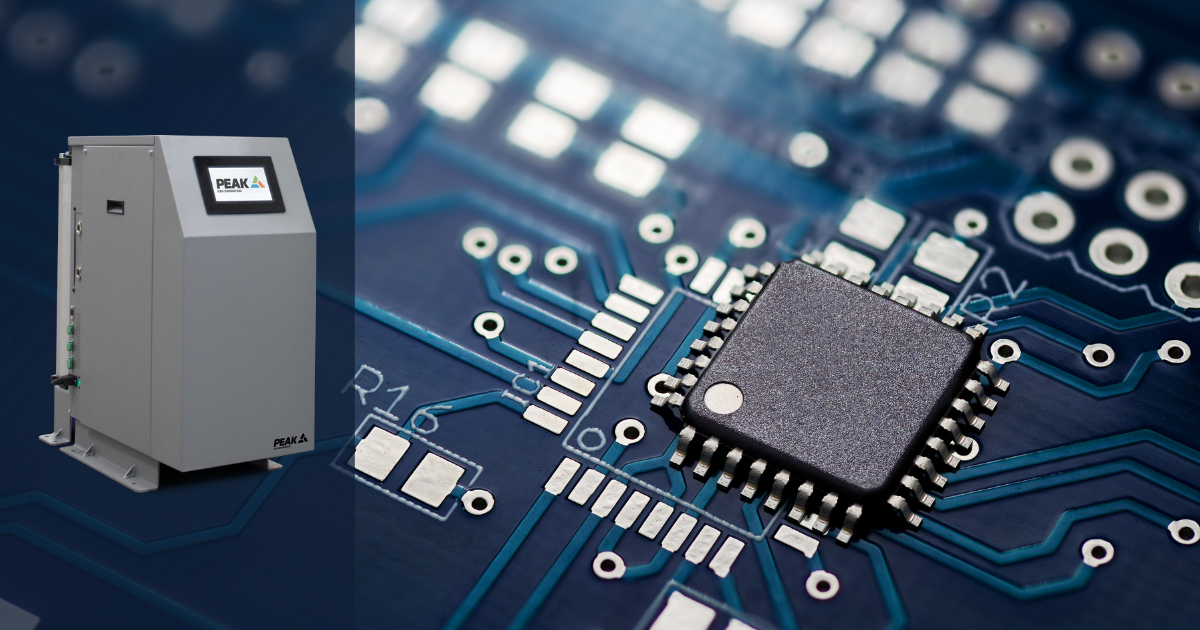
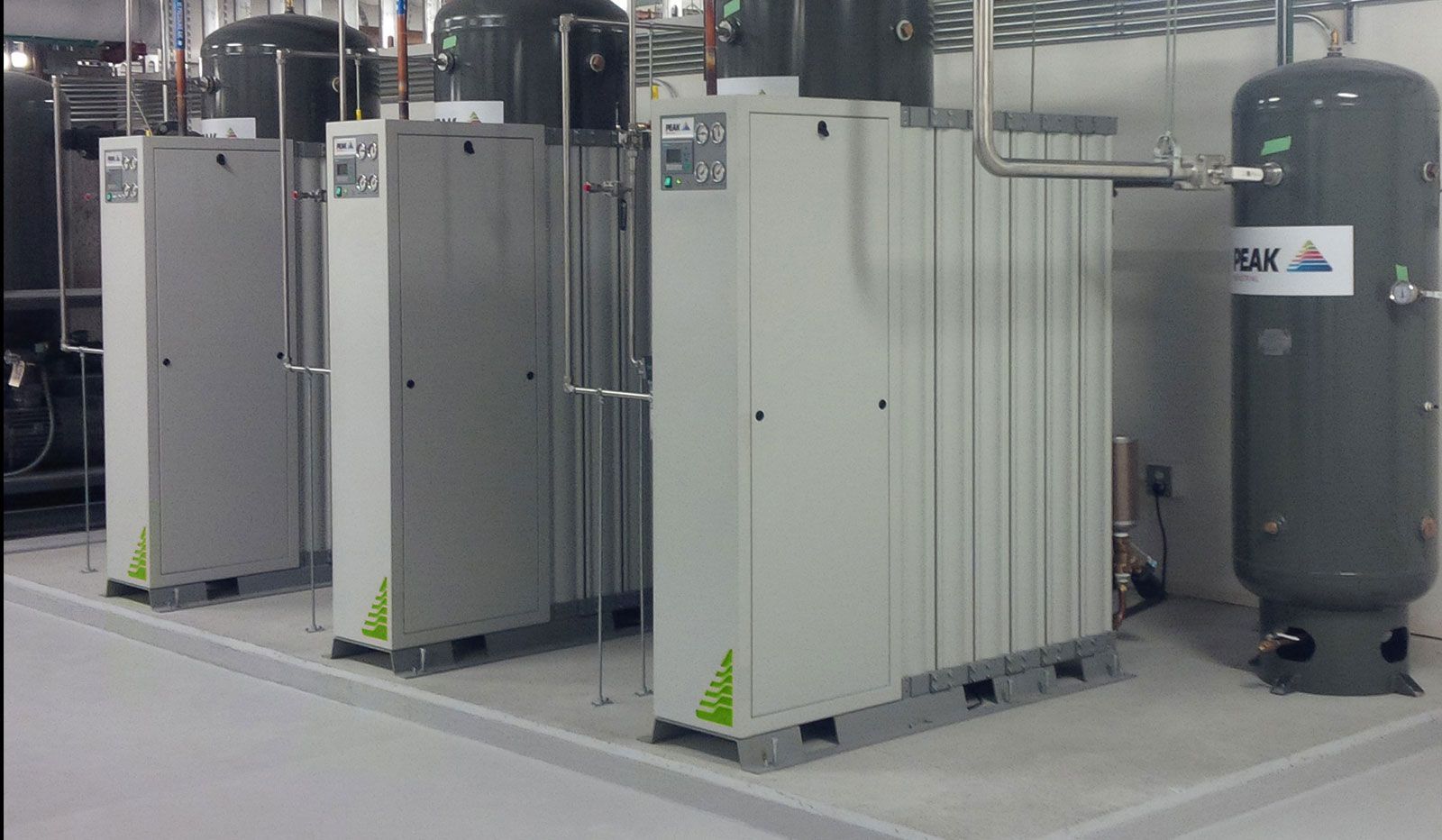